Understanding the Role of Rotomolding in Custom Plastic Production
Understanding the Role of Rotomolding in Custom Plastic Production
Blog Article
Rotational molding, or Rotomolding, has become a chosen manufacturing technique for making tough and high-quality plastic parts. Its distinctive process, which requires heating and rotating components in the shape, assures equally spread energy and reliability in the final product. This blog considers the unbelievable benefits of Rotomolding and why it's gained prominence as a strategy for making tough and long-lasting plastic components.
Remarkable Energy with Uniform Wall Width
One of the crucial strengths of rotomolding lies in its ability to produce components with uniform wall thickness. Unlike other production strategies that'll leave bumpy or thin parts vulnerable to weakness, rotomolding ensures uniformity atlanta divorce attorneys layer. By consistently heat and spinning the form, the molten resin moves easily, creating seamless and powerful plastic areas that will withstand large loads and avoid impact.

This feature makes rotomolded areas suitable for applications requesting structural reliability, such as for example large tanks, playground equipment, and industrial containers.
Enhanced Toughness with Stress-Free Molding
Pressure may destroy plastic parts, impacting their life and performance. Luckily, the rotomolding method eliminates central stresses usually found in different molding techniques. Because no high-pressure causes are used all through manufacturing, the plastic-type material experiences minimal pressure, causing a stronger solution that functions easily around time.
Additionally, the lack of seams or weld lines increases the general toughness of rotomolded pieces, making them resistant to breaking, splitting, and environmental wear and tear.
Excellent Mobility and Customization
Rotomolding offers unparalleled style flexibility, letting producers to create complex styles and structures with precision. The ability to integrate added characteristics like ribs, inserts, or structure guarantees that the ultimate solution meets certain useful or visual requirements.
This technique also helps the use of a wide selection of materials and chemicals, such as for instance UV stabilizers and colorants, more improving toughness by making parts resilient to factors like sunlight exposure, fading, and compound damage.
Resilience in Severe Conditions
Rotomolded pieces are built to last, even when subjected to severe environments. They keep their reliability in hard temperatures, avoid rust from compounds, and experience extended outdoor use. This makes them specially useful in industries like agriculture, construction, and maritime applications, wherever components experience difficult problems daily.
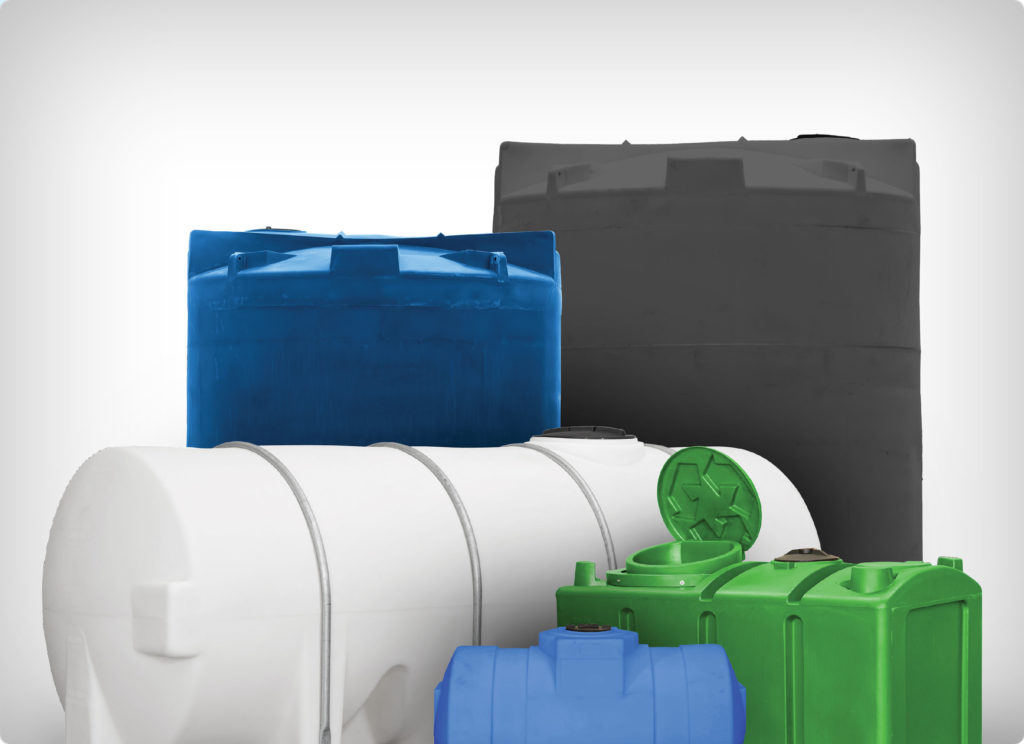
Their ability to perform dependably such situations decreases the necessity for regular substitutes, creating rotomolded parts equally cost-effective and sustainable.
Operating the Future of Resilient Parts
The increasing need for trusted and resilient plastic pieces remains to place rotomolding at the front of production innovation. Having its accuracy, stress-reducing benefits, and capability to resist diverse conditions, rotomolding is surrounding the way in which industries prioritize energy and durability within their products. By purchasing this advanced process, companies may generate plastic parts that stay the check of time.
Report this page