How Plastics Rotomolding Supports the Creation of Durable, Hollow Parts
How Plastics Rotomolding Supports the Creation of Durable, Hollow Parts
Blog Article
Parts rotomolding, or rotational molding, is a manufacturing method that's received immense reputation because of its capacity to produce durable, empty elements with outstanding precision. From large professional tanks to little custom components, this approach is noted for its flexibility and efficiency. Under, we'll investigate the key benefits of Parts Rotational Molding and why it's develop into a preferred alternative for making high-quality, empty parts.
What's Plastics Rotomolding?
Rotomolding is a production process that involves heat plastic material inside a rotating mold. This permits the molten plastic to coat the interior areas of the form consistently, creating worthless parts with an easy structure. The effect? Something that is not merely resilient but also amazingly adaptable, giving endless applications across industries.

Crucial Advantages of Materials Rotomolding
1. Strength and Longevity
One of many standout features of plastics rotomolding could be the unparalleled longevity it offers. Rotomolded elements are made to resist intense situations, including large influences, tough weather, and compound exposure. This energy makes rotomolded areas ideal for purposes in industries like automotive, agriculture, and construction.
The seamless, single-piece structure also plays a part in the architectural reliability of rotomolded products. Unlike other strategies, you can find no seams or disadvantages, lowering the danger of breaks or leaks.
2. Cost-Effective Manufacturing
Rotomolding is highly cost-effective, especially when making large or complex worthless parts. The procedure requires fairly low tooling prices compared to different production strategies, such as procedure molding or hit molding. That causes it to be particularly ideal for small-to-medium manufacturing runs without reducing quality.
Also, the ability to create areas with consistent wall thickness decreases material spend, optimizing cost-efficiency actually further.
3. Style Flexibility
The flexibility of rotomolding opens the entranceway to extremely personalized designs. Whether it's complex forms, undercuts, or varying wall thicknesses, rotomolding enables suppliers to show also the absolute most complex designs in to reality. That freedom is critical for industries that need precision and versatility within their components.
Further customization possibilities include bumpy surfaces, embedded inserts, and also multi-layered parts for added padding or strength.
4. Lightweight However Powerful
Rotomolded elements achieve the right balance between weight and durability. The useless structure diminishes product use, ensuring products remain lightweight while sustaining their structural strength. That is especially necessary for areas such as outdoor gear, tanks, or playground structures, wherever simple transportation and installation are key considerations.
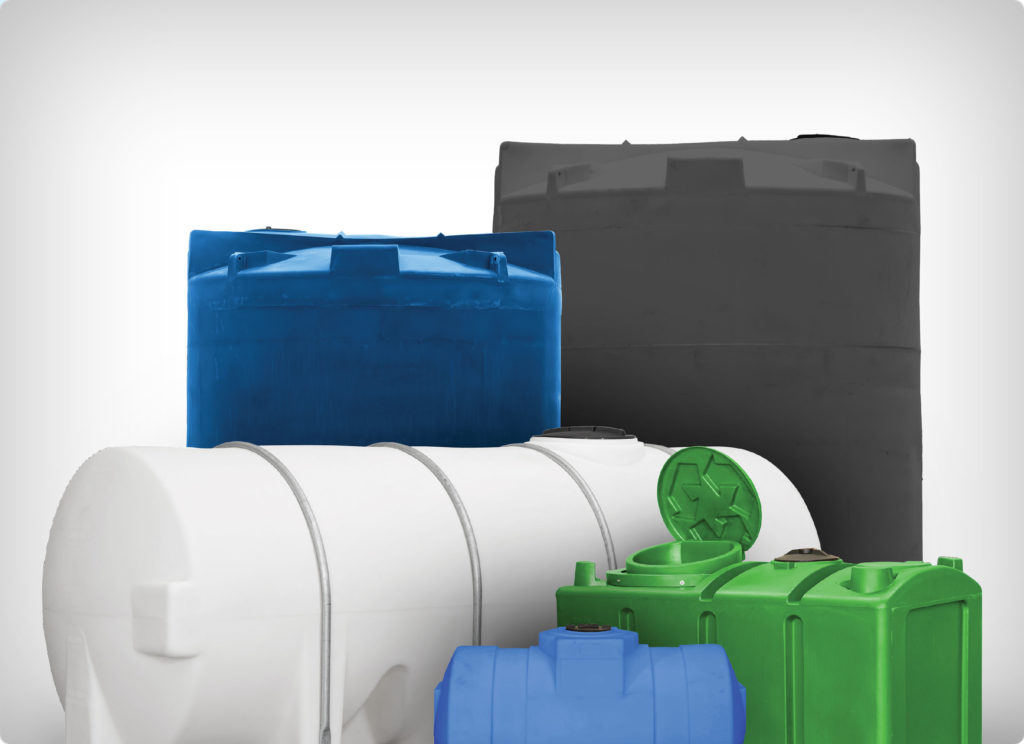
5. Eco-Friendly Production
Rotational molding is also widely celebrated for the environmental benefits. The process results in little product spend, as plastic products can often be reused or recycled. Additionally, makers can use eco-friendly materials to align with sustainability goals. This jobs rotomolding as an significantly appealing choice for businesses seeking to reduce their environmental impact.
Why Plastics Rotomolding Stands Out
Parts rotomolding has changed the generation of sturdy, hollow areas by supplying a special mixture of strength, cost efficiency, and style flexibility. By leveraging this process, suppliers can supply top quality areas that meet the precise demands of numerous industries while encouraging an eco-conscious method of production.
If you're buying a manufacturing process that offers smooth durability and irresistible accuracy, rotomolding could be the answer.
Report this page